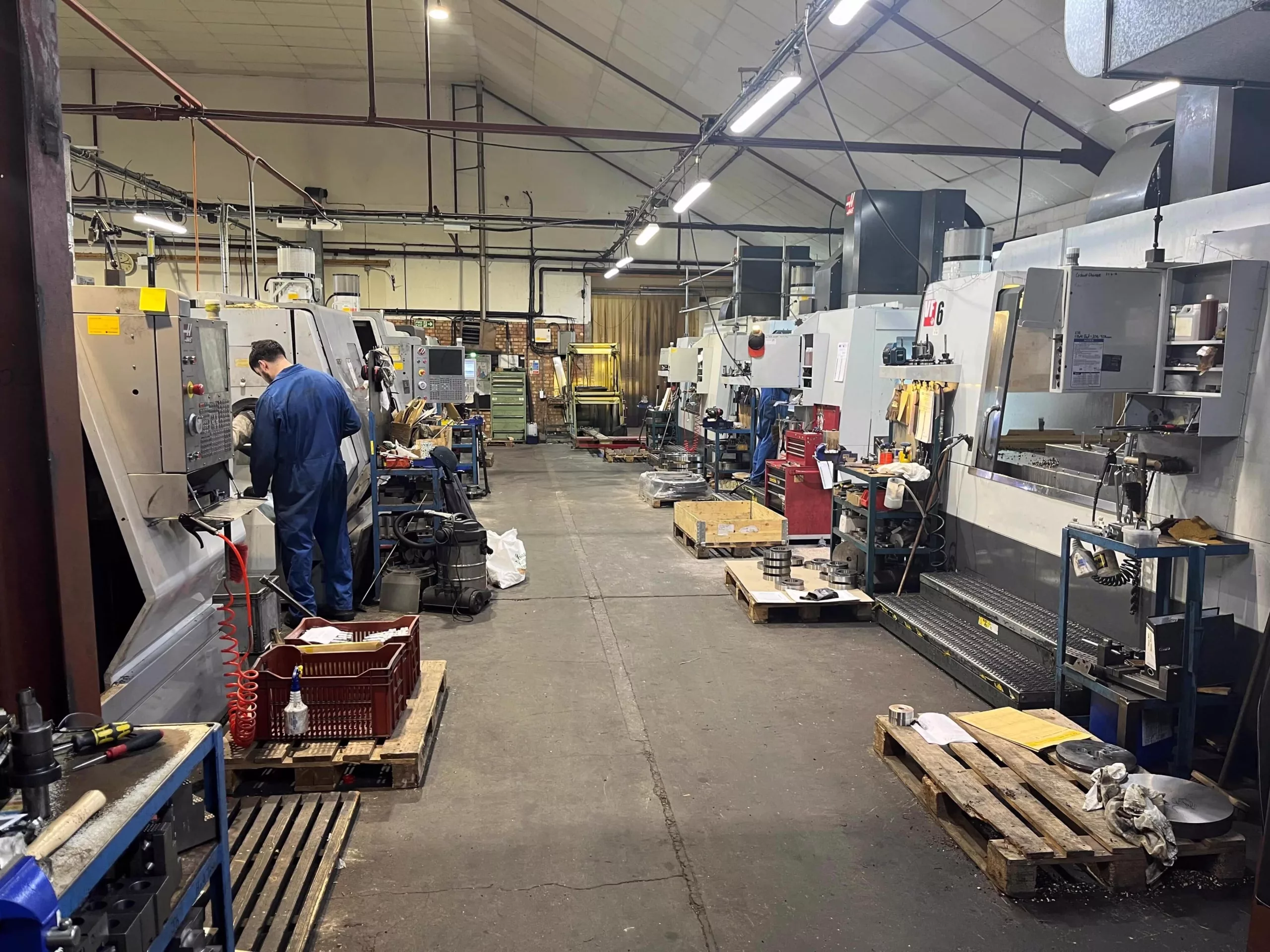
The Challenge
The client in this case study approached Polgain Limited seeking ways to reduce costs in their machining processes. The primary goal was to optimise material usage while maintaining production efficiency and precision.
Our Approach
We tackled this challenge by offsetting the work in our CNC lathe chuck using custom fixturing. This approach aimed to reduce material waste and enhance machining efficiency.
Overcoming Challenges
During implementation, we encountered out-of-balance vibrations due to the offset workholding. To counteract this, we developed and integrated a counterweighted turning fixture, ensuring smooth operation and maintaining machining accuracy.
The Process & Results
To validate the efficiency of the new method, we conducted a thorough investigation, calculating material removal requirements and optimising billet sizing. Using OneCNC software, we designed a 3D model and employed volume verification tools to determine material savings.
Key Findings:
- Switching from 212mm billets to 172mm billets significantly reduced waste.
- The mass of removed material decreased from 6.129kg to 2.825kg per billet.
- This change eliminated 3.304kg of waste per part, minimising material costs and reducing cutting tool wear.
By implementing this method, we not only reduced raw material usage but also enhanced tool longevity and lowered cutting fluid consumption, further driving down operational costs.
Timeframe & Implementation
The project was an ongoing procedure spanning several months, involving rigorous trials before committing to bulk material purchases. Despite the extended testing phase, the final implementation successfully met the project’s cost-reduction objectives.
Conclusion
Through innovative fixturing and strategic billet selection, Polgain Limited delivered a tangible and sustainable cost-saving solution, reducing waste and optimising machining processes without compromising quality or precision. This case study showcases our commitment to precision engineering and continuous improvement in manufacturing efficiency.